
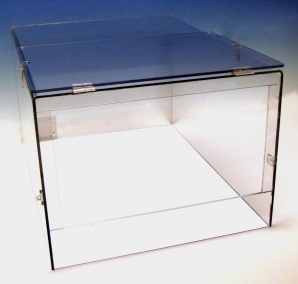
In contrast to previous publications on the modeling of riser reactors for catalytic cracking, the current mode includes a fundamental description of the reaction pathway to catalytic coke, resulting in a slightly higher. The negative effect of temperature on the experimentally observed coking rates is qualitatively described and is explained in terms of an overcompensation of the increase of the rate coefficient by a lower surface coke precursor concentration.Ī relumped Single-Event MicroKinetic model for the catalytic cracking of hydrocarbons and coke formation on a RE-USY equilibrium catalyst is used to simulate an industrial riser. The activation energies for these alkylations obtained via non-isothermal regression are independent of the feedstock within the parameters confidence limits reflecting the fundamental character of the SEMK. The bulky alkylated species formed out of these alkylations are considered as coke. Three types of irreversible alkylations involving both gas phase and surface coke precursors, viz., alkylation of phenyl substituted carbenium ions with C3–C5 alkenes, alkylation of the nucleus of monoaromatics with C3–C5 alkylcarbenium ions, and alkylation of C8–C10 alkylcarbenium ions with C3–C5 alkenes, have been considered as rate-determining steps in coke formation.
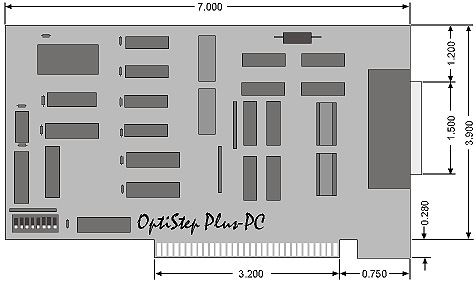
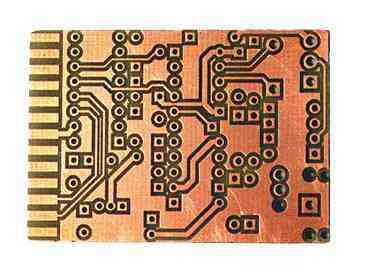
A single-event microkinetic model (SEMK) is applied to model initial coking rates during the catalytic cracking of (cyclo)alkane/1-octene mixtures at 693–753 K and (cyclo)alkane and 1-octene inlet partial pressures of 26.6 and 4.8 kPa on a REUSY equilibrium catalyst.
